The Revolution of Surface Mount Technology: Advancements, Applications, and Future Trends
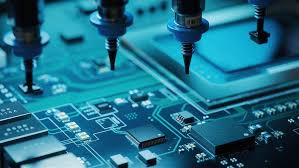
Introduction:
Surface Mount Technology (SMT) has emerged as a cornerstone in modern electronics manufacturing, revolutionizing the way electronic components are assembled onto printed circuit boards (PCBs). In this comprehensive exploration, we delve into the intricacies of SMT, its evolution, applications across industries, and the promising future it holds.
Evolution of Surface Mount Technology:
Before the advent of SMT, electronics manufacturing relied on through-hole technology, which involved mounting components by inserting leads into holes on the PCB and soldering them onto the other side. However, as electronic devices became smaller, lighter, and more sophisticated, the limitations of through-hole technology became apparent. SMT emerged in the 1960s as a more efficient and cost-effective alternative.
SMT involves mounting electronic components directly onto the surface of the PCB, eliminating the need for leads and holes. This allows for denser packing of components, reduced size and weight of devices, and improved electrical performance. The evolution of SMT has been characterized by advancements in materials, equipment, and processes, enabling higher levels of automation, precision, and reliability.
Components of Surface Mount Technology:
At the heart of SMT are electronic components specifically designed for surface mounting. These components come in various shapes, sizes, and configurations, ranging from resistors and capacitors to integrated circuits (ICs) and microcontrollers. Key components of SMT include:
Surface Mount Devices (SMDs):
These are electronic components designed for direct placement onto the surface of PCBs. SMDs come in standardized packages such as quad flat packages (QFP), small outline integrated circuits (SOIC), and ball grid arrays (BGA), among others.
Solder Paste:
Solder paste is a mixture of solder alloy particles and flux, used to create electrical connections between SMDs and PCBs. It is applied to the surface of the PCB using a stencil, and the components are then placed onto the paste before reflow soldering.
Reflow Soldering:
Reflow soldering is the process of heating the solder paste to a liquid state, causing it to bond the SMDs to the PCB. This process typically involves a conveyor oven with controlled temperature profiles to ensure proper soldering without damaging the components.
Surface Mount Equipment:
SMT assembly lines are equipped with specialized machinery for component placement, solder paste application, soldering, inspection, and testing. These machines range from pick-and-place robots and solder paste printers to reflow ovens and automated optical inspection (AOI) systems.
Applications of Surface Mount Technology:
The versatility and scalability of SMT have led to its widespread adoption across various industries, including:
Consumer Electronics:
SMT is ubiquitous in consumer electronics devices such as smartphones, tablets, laptops, and televisions. The compact size and high component density made possible by SMT enable manufacturers to produce sleeker and more feature-rich products.
Automotive Electronics:
The automotive industry relies on SMT for the assembly of electronic control units (ECUs), sensors, infotainment systems, and advanced driver assistance systems (ADAS). SMT enables the integration of complex electronics into vehicles while meeting stringent reliability and durability requirements.
Medical Devices:
SMT plays a crucial role in the manufacturing of medical devices and equipment, including pacemakers, insulin pumps, diagnostic instruments, and wearable health monitors. The miniaturization and high precision afforded by SMT contribute to the development of cutting-edge medical technologies.
Aerospace and Defense:
In aerospace and defense applications, where reliability and performance are paramount, SMT is preferred for its ability to withstand harsh environments, vibration, and thermal cycling. SMT components are used in avionics, radar systems, missile guidance systems, and satellite communications.
Future Trends in Surface Mount Technology:
As technology continues to evolve, several trends are shaping the future of SMT:
Miniaturization:
The demand for smaller, lighter, and more portable electronic devices is driving the ongoing miniaturization of components and PCBs. SMT will continue to play a crucial role in meeting these demands while maintaining performance and reliability.
High-Speed and High-Frequency Applications:
With the proliferation of high-speed data transmission and wireless communication technologies, there is a growing need for SMT components capable of operating at higher frequencies and bandwidths. This requires advancements in materials and design to minimize signal loss and electromagnetic interference.
3D Integration:
3D integration techniques, such as chip stacking and package-on-package assembly, are being explored to further increase component density and functionality. By vertically stacking multiple layers of components, SMT can achieve even greater levels of integration and performance.
Sustainability and Green Manufacturing:
Environmental concerns are driving efforts towards sustainable and eco-friendly manufacturing practices in the electronics industry. SMT manufacturers are exploring recyclable materials, lead-free soldering processes, and energy-efficient production methods to reduce their carbon footprint.
Conclusion:
Surface Mount Technology has revolutionized the electronics manufacturing industry, enabling the production of smaller, lighter, and more sophisticated devices across a wide range of applications. With ongoing advancements in materials, processes, and design, SMT is poised to continue driving innovation and shaping the future of electronics for years to come. As technology evolves and new challenges arise, SMT will remain at the forefront of electronic component assembly, pushing the boundaries of what is possible in the world of electronics.